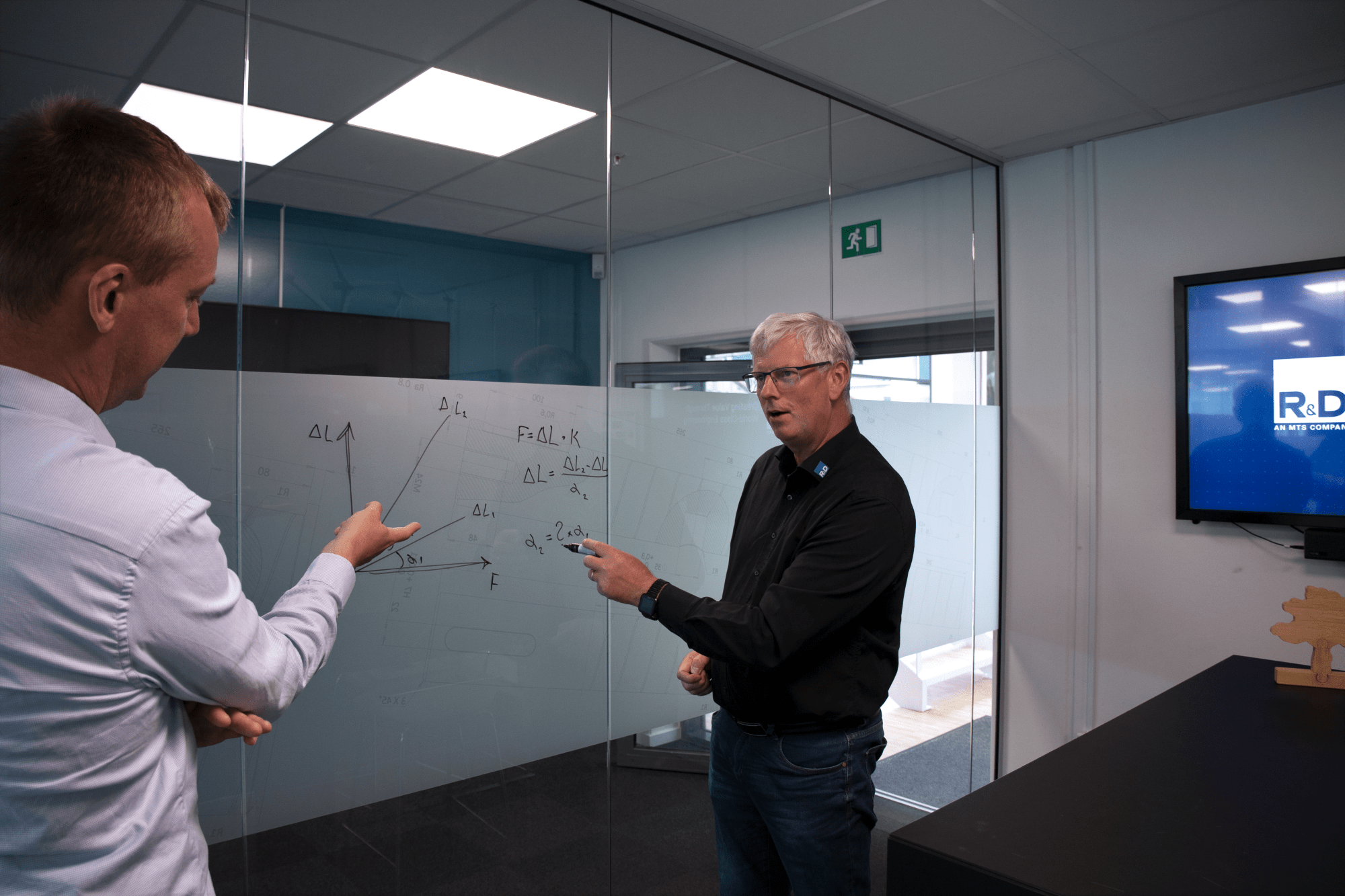
Leidenschaft für Sicherheit führte zu Aha-Erlebnis: Erfindung eines Werkzeugs zur Überprüfung der Bolzenspannung von Windkraftanlagen
Leidenschaft für Sicherheit führte zu Aha-Erlebnis: Erfindung eines Werkzeugs zur Überprüfung der Bolzenspannung von Windkraftanlagen
Die Leidenschaft für Sicherheit brachte den dänischen Ingenieur Flemming Selmer Nielsen - oder "Mr. Bolzen", wie er liebevoll unter Kollegen genannt wird - nachts um halb zwei auf die Idee für ein Werkzeug zur Überprüfung der Schraubenspannung von Windkraftanlagen. Diese frühmorgendliche Offenbarung liegt nun vier Jahre zurück, und im vergangenen Jahr wurde für seine Erfindung ein Patent erteilt.
Eine falsche Bolzenspannung kann zum Ausfall der gesamten Windkraftanlage führen, wie Flemming Selmer Nielsen nur zu gut weiß. In seinem früheren Job bei einem großen Windkraftanlagenhersteller hat er schon alles gesehen, auch einen Einsturz. Immer schon hatte ihn gestört, dass es kein einfaches und effektives Messinstrument gab, um die sicherheitskritische Spannung in den Schrauben direkt zu messen.
Als er bei R&D, einem dänischen Experten für Windturbinenprüfgeräte, anfing, konzentrierte Flemming Selmer Nielsen seine kreative Energie auf die Lösung des Problems der genauen Messung der Schraubenspannkraft
Falsche Spannkraft in Windturbinen ist eine häufige Komplikation, die unnötige Kosten und Ausfallzeiten nach sich zieht und im schlimmsten Fall zum Ausfall der gesamten Windkraftanlage führen kann. Sie entsteht durch die relativ geringe Genauigkeit der herkömmlichen Werkzeuge, oder auch durch manuelle Fehler.
Nachdem Flemming Selmer Nielsen mehr als ein Jahr lang an der Lösung gearbeitet hatte, kam ihm die Idee wie ein Blitz aus heiterem Himmel.
„Ich bin mitten in der Nacht aufgewacht", erklärt Flemming Selmer Nielsen mit leuchtenden Augen „Ich war hellwach und hatte eine klare Vorstellung von der genauen Formel, wie man die Spannkraft eines Bolzens in einer Windkraftanlage genau bestimmen kann. Diese Idee von vor vier Jahren ist das Prinzip des Bolt-Check-Systems, das unsere Kunden heute verwenden“, sagte der Erfinder.
„Ich konnte den Rest der Nacht nicht mehr schlafen: Erstens, war ich so aufgeregt, dass ich es geknackt hatte. Und zweitens enthielt die Offenbarung, die ich hatte, die genaue mathematische Formel, die die Grundlage des Patents bildet. Als meine Frau morgens aufwachte, verstand sie gar nicht, was da passiert war und was ich gerade zu Papier gebracht hatte", erzählt Flemming Selmer Nielsen.
„Die Lösung bestand in der Kombination von Ultraschall- und physikalischen Messungen der Schraube, wobei die Spannung in der Schraube allein durch die Kenntnis der Differenz zwischen diesen beiden Messungen bestimmt werden kann", fügt Flemming Selmer Nielsen hinzu.
Indirekte versus direkte Messungen
„Die Verwendung eines Drehmomentschlüssels oder eines Spannwerkzeugs zum Anziehen einer Schraube liefert indirekte Messungen der Spannkraft", erklärt Flemming Selmer Nielsen. „Unser System misst direkt die Dehnung der Schrauben, die auftritt, wenn eine Schraube unter Spannung steht, und das ist ein wesentlicher Unterschied“, fügt Flemming Selmer Nielsen hinzu.
Die direkte Messung mit Bolt-Check erreicht eine viel größere Genauigkeit als beispielsweise mit einem Drehmomentschlüssel.
„Das bedeutet, dass wir es uns erlauben können, die Schrauben etwas fester anzuziehen, als es sonst möglich ist. Das kann bedeuten, dass wir die Schrauben nur ein einziges Mal nachziehen müssen. Wir können den Wartungsaufwand um die Hälfte reduzieren", sagt Flemming Selmer Nielsen.
„Meiner Erfahrung nach werden Ingenieure oft zur Ursachenanalyse von lockeren oder gebrochenen Schrauben gerufen, und in vielen Fällen liegt es daran, dass die durch das aufgebrachte Drehmoment erzielte Spannkraft nicht ausreicht", kommentiert Flemming Selmer Nielsen. "Bolt-Check zeigt, dass dieses Problem relativ einfach zu lösen ist. Nachdem ich den Einsturz einer Windkraftanlage beurteilen musste, bei dem eine falsche Schraubenspannung eines der Probleme war, bin ich zuversichtlich, dass Bolt-Check in Zukunft einen Beitrag zur Sicherheit leisten kann. Vor allem dann, wenn Windkraftanlagen altern und mehr Wartung benötigen“, schließt er.
Auch die Ingenieure profitieren
Ein weiterer Vorteil von Bolt-Check ist die verbesserte Gesundheit und Sicherheit der Ingenieure, die diese wichtige Arbeit ausführen. Herkömmliche Werkzeuge sind oft schwer und können auch ein Sicherheitsrisiko darstellen, da sie mit hohem Hydraulikdruck arbeiten. Das Bolt-Check-Prüfungsgerät ist in der Lage, mehr als 100 Schrauben pro Stunde zu prüfen. Es ist leicht und handlich und bietet somit erhebliche Verbesserungen in Bezug auf Gesundheit und Sicherheit.
Bolt-Check benötigt keine speziell angefertigten Bolzen, sondern kann mit jedem Bolzen verwendet werden. Dies ist einer der Gründe, warum das System nur einen Bruchteil des Preises einiger anderer sensorgestützter Systeme kostet. Jede überwachte Schraube kann jedoch mit einem eindeutigen Rückverfolgungsetikett versehen werden, das einen detaillierten Dokumentationspfad liefert, der den Standort jeder Schraube sowie ihren Service- und Wartungsplan enthält.
Das Bolt-Check-Werkzeug wurde am R&D-Hauptsitz in Aarhus in Dänemark entwickelt, welches auch das erste Land der Welt war, das eine Windkraftanlage mit drei Rotorblättern in Dienst stellte. Ab 1957 produzierte die Windkraftanlage im süddänischen Gebiet „Gedser“ Strom und sie war richtungsweisend für die modernen Anlagen von heute.
Bolt-Check wurde 2019 auf der Messe Wind Energy Denmark 2019 mit einem Innovationspreis ausgezeichnet und hat die DNV-GL-Produktzertifizierung erhalten, die es erlaubt, das Gerät für Service- und Wartungsinspektionen als Alternative zu Drehmoment- oder Spannwerkzeugen einzusetzen. Das System ist derzeit sowohl in Offshore- als auch in Onshore-Anlagen in Betrieb.
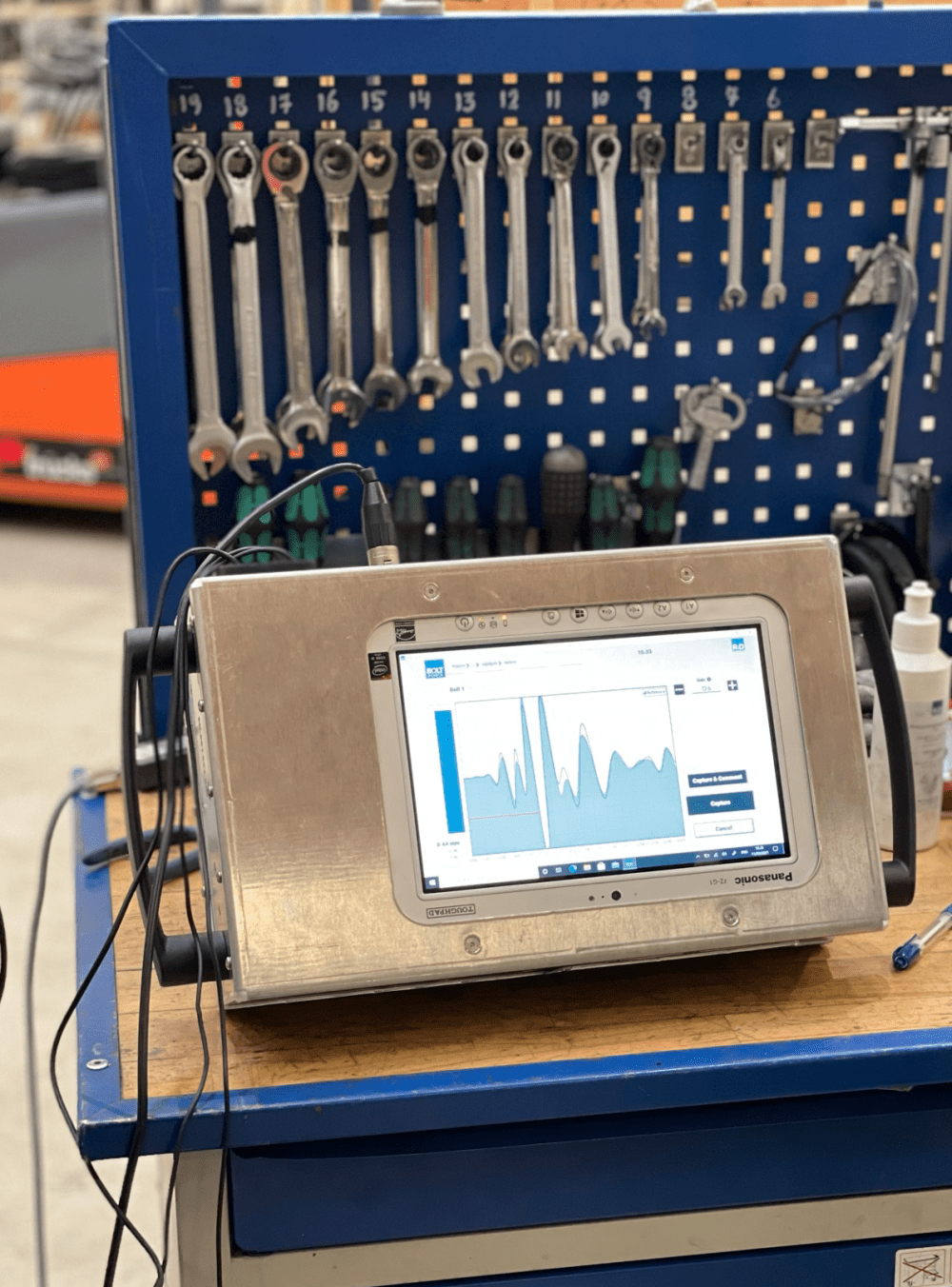